7.1. Общие требования
7.1.1. При сборке руководствоваться общими положениями и требованиями
раздела 1 и, кроме того, следующими требованиями.
7.1.2. СЧ, поступающие на сборку, должны соответствовать требованиям
на дефектацию, техническим условиям на ремонт (восстановление) и конструкторской
документации изготовителя.
7.1.3. Перед сборкой СЧ (кроме прецизионных) топливной аппаратуры
должны быть тщательно промыты, продуты осушенным сжатым воздухом, а непосредственно
перед монтажом трущиеся поверхности - смазаны чистым индустриальным маслом
ГОСТ 17479.
7.1.4. Прецизионные детали плунжерных пар, нагнетательных клапанов,
распылителей форсунок должны быть промыты чистым авиационным бензином
Б-70 ГОСТ 1012 и перед сборкой - смазаны профильтрованным дизельным топливом
ГОСТ 305.
7.1.5. Плунжерные пары для одного ТНВД должны быть одной группы
плотности. Для комплектования в группы для одного насоса все плунжерные
пары (новые и бывшие в эксплуатации) должны подвергаться гидравлическому
испытанию согласно требованиям раздела 9 первой части Руководства. Разница
времени отсечки для плунжерных пар, комплектуемых в одну группу плотности,
не должна быть: для значений времени отсечки от 5 до 10 с. - не более
2 с., свыше 10 до 15 с. - не более 5 с., свыше 15 с. - не более 10 с.
Плунжерные пары с гидравлической плотностью более 40 с. подлежат дополнительной
проверке: смазанная чистым дизельным топливом плунжерная пара устанавливается
верхним торцом втулки на стол (лучше на бумагу, картон); после пятиминутной
выдержки втулка должна при поднятии за плунжер плавно сползать с плунжера
под действием силы собственной тяжести.
7.1.6. Нагнетательные клапаны (новые и бывшие в эксплуатации) перед
комплектованием подлежат контролю согласно требованиям раздела 9 первой
части Руководства. Комплектование нагнетательных клапанов в группы для
одного ТНВД, должно проводиться по величине диаметрального зазора по разгрузочному
пояску. Сортировку клапанов по диаметральному зазору рекомендуется производить
с помощью пневматического длиномера: с конусностью трубки 1:400 при зазоре
от 0,01 до 0,1 мм и сортировке на группы через 0,01 мм и 1:1000 при зазоре
до 0,01 мм и сортировке на группы через 0,002 мм. Клапаны для работы с
новыми плунжерными парами следует подбирать с зазором в пределах 0,004
-0,01 мм с интервалом 0,002 мм. При этом для плунжерных пар с наибольшей
плотностью следует подбирать клапаны с наименьшим зазором. Допускается
комплектование новых плунжерных пар для одного насоса нагнетательными
клапанами с зазором по разгрузочному пояску до 0,07 мм, но с сортировкой
на группы по величине зазора так, чтобы в группе для одного насоса колебание
зазора не превышало 0,01 мм.
7.1.7. Изношенные плунжерные пары для одного насоса следует комплектовать
изношенными нагнетательными клапанами с зазором по разгрузочному пояску
до 0,1 мм, но с сортировкой на группы согласно п. 7.1.6.
7.1.8. При промывке, проверке и установке на насос прецизионных
пар необходимо обеспечить их комплектность; замена одной детали другой
не допускается.
7.1.9. У правильно подобранной пары втулка-шток ТПН (рис.
7.1) втулка, смазанная чистым дизельным топливом, в вертикальном положении
должна перемещаться по штоку плавно без задержек под действием собственной
массы. Проверка должна производиться не менее чем в трех положениях по
углу поворота втулки на штоке
7.1.10. Зазор в сопряжении втулка-шток не должен превышать 0,015
мм. Величину зазора рекомендуется проверять в корпусе насоса замером плотности
сопряжения воздухом по схеме (рис. 7.2).
Предельное состояние следует определять по времени падения давления от
0,5 до 0,4 МПа (5 до 4 кгс/см2) в ресивере объемом 30 см3, подключенном
через герметичный кран к сети сжатого воздуха. Испытание необходимо проводить
в следующем порядке: установить корпус в сборе со втулкой и штоком на
приспособление; заполнить ресивер воздухом до давления не менее 0,55 МПа
(5,5 кгс/см2); герметично отключить ресивер от сети сжатого воздуха; замерить
время, в течение которого происходит падение давления в ресивере от 0,5
до 0,4 МПа (5 до 4 кгс/см2); полученное время сравнить с временем для
эталонной прецизионной пары втулка-шток, имеющей допустимый зазор в сопряжении,
равный 0,015 мм.
7.1.11. При замене пары втулка-шток, новую втулку необходимо установить
в корпус насоса, предварительно очистив резьбовое отверстие корпуса от
остатков клея, обезжирив и смазав резьбу корпуса втулки эпоксидным клеем
или анаэробным герметиком. Втулку ввинтить в корпус моментом 10 Нґм (1
кгсґм) и проверить подвижность штока; при перемещении штока с прихватыванием
необходимо слегка ослабить затяжку втулки.
7.1.12. Герметичность прилегания клапанов насоса к седлам обеспечить
притиркой сопрягаемых поверхностей седла и клапана на доводочной плите
с использованием пасты АСМ 2/1 НОМ ГОСТ 25593. Притирку проводить вручную
петлеобразными движениями.
7.1.13. После запрессовки в корпус какие-либо повреждения на притертой
поверхности седла не допускаются.
7.1.14. Шероховатость Rа поверхности отверстий корпуса ТПН и цилиндра
под поршни и поршней не должна быть более 0,8 мкм, отверстия корпуса под
толкатель и толкателя - не более 1,25 мкм.
7.1.15. Поршни подкачивающего и ручного насосов должны свободно
перемещаться в своих цилиндрах, заедание не допускается. Клапаны и толкатель
должны свободно, без заедания перемещаться под действием пружин. Ролик
толкателя должен вращаться легко, без заедания. Ход поршня насоса ручной
прокачки в цилиндре должен быть плавным по всей длине цилиндра.
7.1.16. Перед сборкой насоса трущиеся поверхности составных частей
необходимо смазать дизельным топливом.
7.1.17. Пробки и цилиндр ручной прокачки следует ввинчивать в корпус
насоса, предварительно смазав резьбу герметизирующей пастой.
7.1.18. Перед сборкой ТНВД тщательно проверить состояние опорной
поверхности отверстий секций корпуса под заплечики втулки плунжера; задиры,
риски, черновины, смятие и трещины не допускаются. При наличии задиров,
рисок, черновин и смятия допускается восстанавливать поверхность обработкой
(зенкованием) до выведения дефектов с обеспечением шероховатости не более
1,25 мкм, выполнением галтели радиусом 0,2 -0,3 мм и на глубину не более
0,5 мм.
7.1.19. Шероховатость поверхностей отверстий (пазов) корпуса под
толкатели и рейку должна быть 1,25 мкм, кулачков кулачкового вала - 0,63
мкм, толкателей - 1,25 мкм.
7.1.20. После установки оси втулка и ролик толкателя должны вращаться
свободно, без заеданий.
7.1.21. При сборке кулачкового вала маслоотражательная шайба подшипника
должна быть обращена выпуклой стороной наружу (к концам вала).
7.1.22. При установке внутренних колец конических роликоподшипников
на кулачковый вал и наружных колец в переднюю крышку (или установочный
фланец) и заднюю крышку (или корпус регулятора) необходимо проверить их
посадку до упора.
7.1.23. После установки кулачкового вала и затяжки крепления подшипников
проверить осевой люфт вала индикаторным приспособлением при приложении
усилия 50 -60 Н (5 -6 кгс). Вал должен прокручиваться от усилия руки свободно,
без заеданий. Значения осевого люфта даны в требованиях на сборку каждой
мод. ТНВД.
7.1.24. Толкатели плунжеров должны без заеданий под действием собственной
массы перемещаться в расточках корпуса.
7.1.25. При установке втулки плунжера в корпус (головку) насоса
удары по ее торцу металлическим предметом не допускаются. После закрепления
стопорным винтом втулка плунжера должна иметь зазор по всей длине паза
без провертывания вокруг своей оси. Отсутствие зазора и тугое перемещение
втулки не допускаются.
7.1.26. После затяжки штуцера секции перемещение плунжера во втулке
должно быть без местных прихватываний и ощутимого усилия при повороте
плунжера на любой угол относительно втулки; перемещение плунжера необходимо
проверить не менее чем в трех положениях по углу поворота плунжера относительно
втулки.
7.1.27. Рейка в отверстиях (пазах) корпуса насоса должна перемещаться
легко, без заеданий на всей длине хода рейки.
7.1.28. Собранные с державкой (ступицей) грузы регулятора должны
свободно, без заеданий качаться на осях. Грузы должны быть одной группы
по массе (с разницей не более 2 г.) или статическому моменту. 7.1.29.
В собранном регуляторе все подвижные составные части должны перемещаться
без заеданий. Рейка должна без прихватываний перемещаться при повороте
рычага управления регулятором и вращении кулачкового вала.
7.1.30. Топливные каналы корпуса после сборки ТНВД следует прокачать
чистым дизельным топливом, отверстия штуцеров секций и ТПН закрыть технологическими
заглушками.
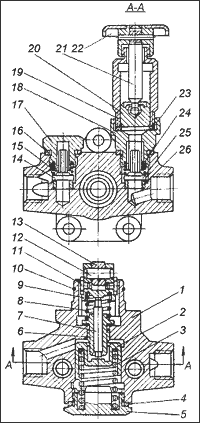
Рис. 7.1. Топливоподкачивающий насос:
1 - корпус; 2 - поршень; 3, 8, 15 - пружины; 4, 16 - уплотняющая шайба;
5, 17 - пробки; 6 - втулка;
7, 21 - штоки; 9 - толкатель; 10 - стопорное кольцо толкателя; 11 - сухарь
толкателя; 12 - ось ролика;
13 - ролик; 14 - нагнетательный клапан; 18 - корпус цилиндра ручного насоса;
19 - цилиндр ручного насоса; 20 - поршень; 22 - рукоятка; 23 - прокладка;
24 - втулка; 25 - всасывающий клапан;
26 - седло клапана.
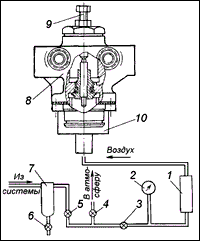
Рис. 7.2. Схема установки для испытаний пары шток-втулка:
1 - воздушный аккумулятор; 2 - манометр; 3, 4, 5, 6 - краны; 7 - масловлагоотделитель;
8 - корпус насоса;
9 - ограничитель перемещения штока; 10 - соединитель для подвода воздуха
к корпусу насоса.
Содержание
|